World’s First
Characteristics of new method
A higher fill factor and higher reliability can be achieved with the Cassette Method, ideal for high efficient EV drive motor. Video prepared below
Differences with conventional wire inserter methods
Conventional Inserter Type challenge
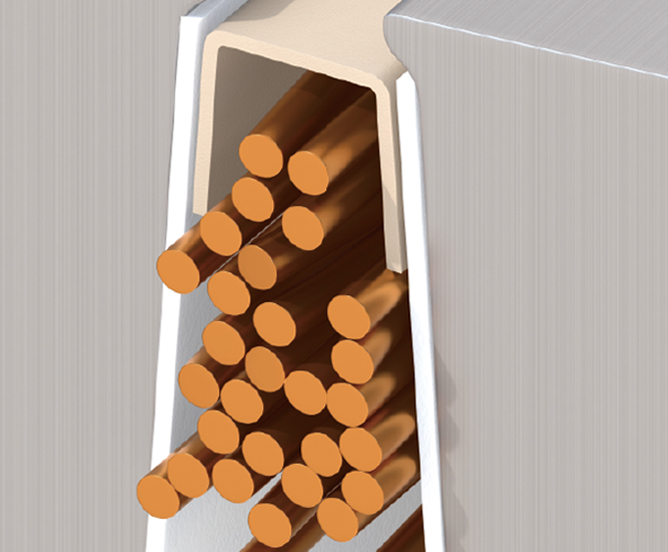
The fill factor is limited to about 45%
(copper wire)
Wire crossing occurs inside the slot.
New Cassette Method solutions
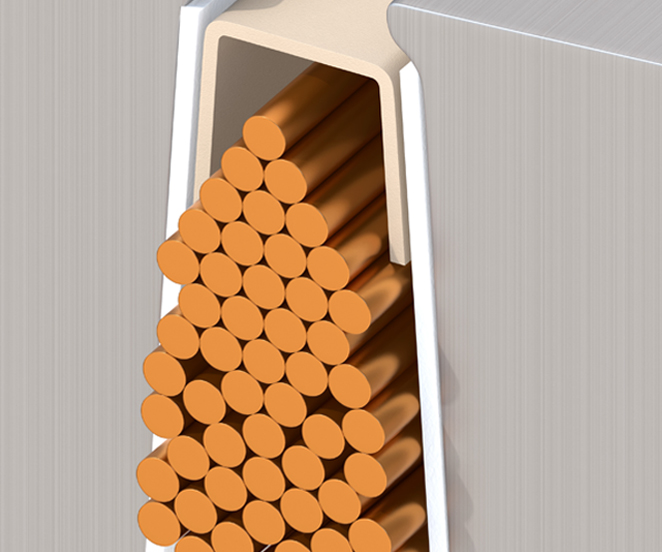
Achieve a high fill factor rate of 50% or more
(copper wire)
Perfect layer windings are passed cleanly into the slot, so that the alignment is improved and the fill factor is increased.
Conventional Inserter Type challenge
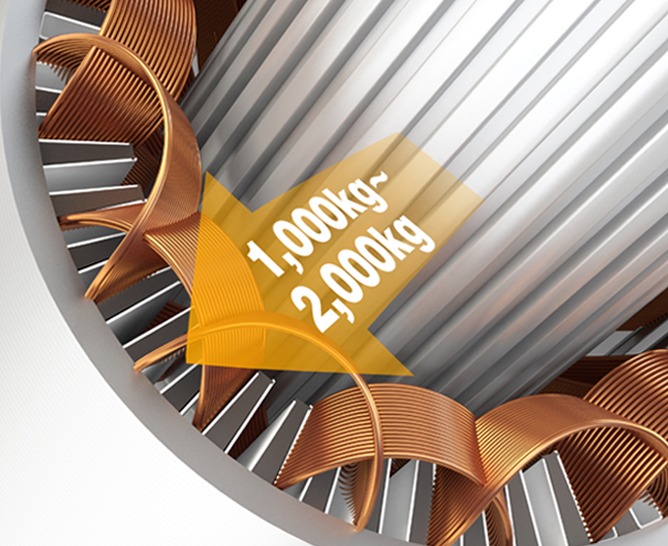
Low rate of scrap at production
The load applied when inserting the wire into the slot can be 1,000kg or more, resulting in damage to the wire.
New Cassette Method solutions

Achieve a high fill factor rate of 50% or more
(copper wire)
Due to a reduced force of approx. 10kg when the wire is inserted, damage to wire is greatly limited.
Conventional Inserter Type challenge

When the wedge is inserted, the coils can be pushed between the slot liner and the wedge, and the insulation distance is reduced.
New Cassette Method solutions
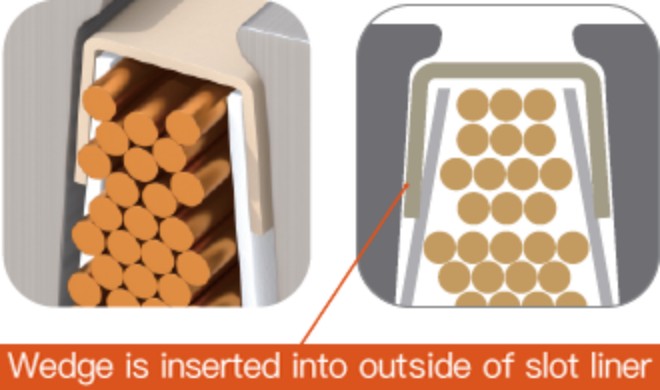
Possibility of further improvement of the fill factor
Only requires pushing coils on ends during wedge insertion.
Ensuring insulation distance for high voltages
Concept that helps prevent coils from moving during wedge insertion.
Solutions to other challenges of winding
Challenges
●Higher coil ends and low efficiency
●Cannot be lap wound in two layers
Solutions
●Low coil end and high efficiency
●High controllability achieved by double-layered winding
※We are accepting prototype requests. Please inquire for details.
Technology partner: Hayashi Industries
Technology & Examples
- Tension Technology
- Winding Technology
- Wire Connection (fusion welding)
- Stripping Technology
- Cutting Technology
- Other Core Technology
- Part Feeding Technology
- Robotic Handling Technology